Introduction to production process
This production process uses mechanized stranding cage for feeding. It has no requirements for the raw materials of sludge (no impurities ≥ 5CM). It is simple and convenient, saves labor and time, reduces costs and improves efficiency.
1. Feeding: (a fully enclosed silo is set)
After the materials are fed into the silo by the elevator, start the feeding valve and feeding auger, and uniformly enter the auger or hydraulic feeder according to the set standard, and use the feeder to feed the materials into the cracking kettle.
2. Pyrolysis
Cracking, set temperature 350 ℃ - 470 ℃. The rotation speed of the cracking kettle is 150 seconds per circle. After the completion of the oil sludge cracking, the residue enters the slag extractor, which sends the residue into the water-cooled slag bin. The residue is automatically put into a ton bag from the high temperature to the normal temperature and packaged for temporary storage.
3. Heating, pressure control
More environment-friendly fuel gas is used for heating. High temperature cracking is equipped with four 30w fuel engines and four gas spray guns, all of which are intelligently controlled to ensure the normal temperature required for cracking production.
The production design pressure of the equipment is normal, the normal production pressure is 0.01MPa - -0.02MPa, and the maximum set pressure is 0.03MPa. During the production process, the pressure control sensor provides the pressure sensing signal. The pressure control system opens or closes the pressure relief control valve according to the set pressure, and sends out an alarm reminder to ensure the safe production of the equipment.
3.4 Production process
Before production, check whether the electric drive device is normal, including (circuit, reducer, blower, induced draft fan, circulating water pump), whether the feeding winch and the discharging winch operate normally, and whether the intelligent power distribution cabinet has any fault (contact the maintenance personnel before failure, and do not start it directly)
Feeding stage
Production stage: before production, check whether the fuel engine, air pump, air compressor and blower are normal, check whether the water seal is short of water, keep the air outlet valve of the winch open, keep the slag outlet valve closed, and keep the vent valve of the steam drum open, and then make the furnace rotate forward for about 100 seconds/circle through the operation of the intelligent power distribution cabinet. When the fuel engine is opened to raise the temperature by 50 ℃, close the vent valve of the gas distributor, Slowly raise the temperature to 150 ℃ - 240 ℃, and the non condensable gas starts to be generated. It is sent to the furnace for combustion through the fuel gas recovery system. According to the amount of non condensable gas, turn off the number of fuel engines in turn to maintain the state of slow fire. (If the amount of non condensable gas is large, it will be sent to another group of equipment for combustion through manual valves. If other equipment does not need it, the excess non condensable gas can be sent to the secondary combustion chamber), and then slowly rise to 380-450 ℃. Ensure that the cracking is clean. Decrease of non condensable gas,
Nitrogen purging system; It is mainly used to purge the treatment kettle, gas receiver, condenser, oil gas separator and water-cooled slag bin to replace the non condensable gas with nitrogen. Ensure the safety of equipment production.
Slagging system; Before slag discharge, the air outlet valve of the winch cage shall be closed through the intelligent electric cabinet, the ash cooling system shall be opened for transmission, and the circulating water pump shall be opened. When the heavy oil valve is opened, a small amount of heavy oil must be drained first to avoid sticking to the slag discharge cage. Close the heavy oil valve after the heavy oil is drained. The furnace body reverses and starts slag discharge for 1-1.5 hours.
Material of cracking kettle: 316L stainless steel Q245RQ345R national standard boiler steel plate
Pyrolysis kettle size: φ 2800MM*7700MM
Volume and heat exchange area of cracking kettle: 47m3 and 80m2
Condensation mode and heat exchange area: water cooling 90m2
Main structure form: horizontal rotation
System pressure: normal pressure
Equipment area: 50m long, 10m wide and 6m high
Equipment weight: 50-60t
Explosion proof process: all electrical appliances are equipped with YB national standard explosion-proof electrical appliances
Fuel consumption: 600 m of natural gas is consumed per day for continuous type ³/ D requires 500L/D of fuel oil
Power and distribution system: the equipment is equipped with a total power of 46.4 kilowatts.
One intelligent desktop control cabinet is equipped (power control, temperature, pressure digital display alarm, touch screen intelligent valve operation and other functions).
The average hourly power distribution is 30kw, and the daily power distribution is about 500-600 kilowatt hours.
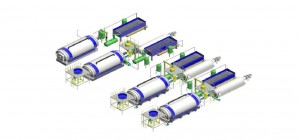
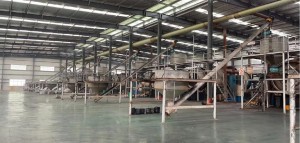
Post time: Jan-09-2023